Unlocking India’s Industrial Salt Potential: Top Manufacturers Shaping the Industry
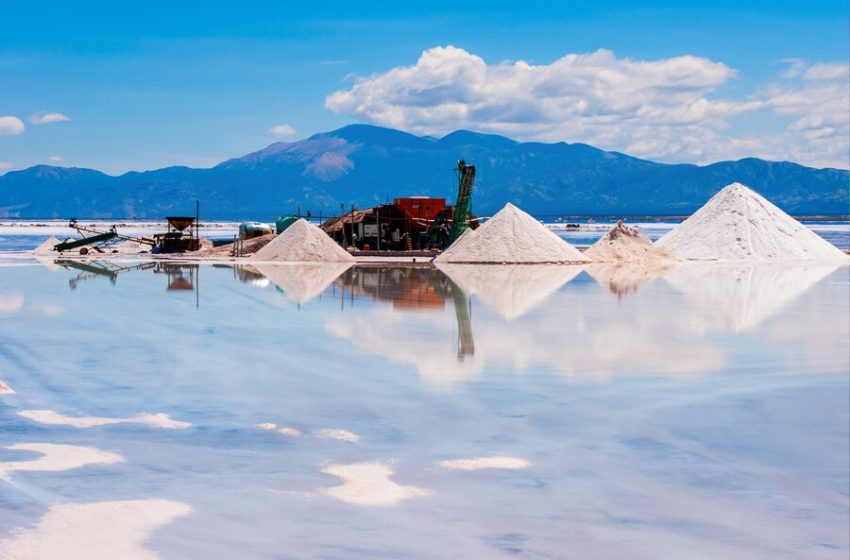
India’s industrial salt industry is a vital part of the global market, supplying high-quality salt for various applications such as chemical production, water treatment, and food processing. With its extensive coastline, favorable climate, and skilled workforce, India has become one of the largest producers and exporters of industrial salt. This blog delves into the potential of India’s industrial salt industry and explores the top manufacturers that are driving the industry forward.
1. The Importance of Industrial Salt
Industrial salt plays a crucial role in numerous industries due to its wide range of applications. It is a key raw material in the production of chlorine, caustic soda, and soda ash—essential chemicals used in manufacturing products like plastics, glass, and detergents. Additionally, industrial salt is used in water treatment, food preservation, and de-icing, making it an indispensable resource for many sectors.
The global demand for industrial salt continues to rise, fueled by industrialization and urbanization. This demand underscores the significance of India’s industrial salt industry, which has positioned itself as a major player on the world stage.
2. An Overview of India’s Industrial Salt Industry
India’s industrial salt industry is deeply rooted in the country’s history, with salt production being a traditional activity along its vast coastline. The majority of industrial salt production is concentrated in the states of Gujarat, Tamil Nadu, and Rajasthan. Gujarat, in particular, accounts for nearly 70% of the country’s total salt production, making it the hub of India’s salt industry.
The success of industrial salt manufacturers in India can be attributed to their adoption of modern technologies and sustainable practices. By integrating these innovations into their production processes, they have been able to enhance efficiency, maintain high standards of quality, and meet the stringent requirements of international markets.
3. Leading Industrial Salt Manufacturers in India
Several industrial salt manufacturers in India have emerged as leaders in the industry, recognized for their commitment to quality, sustainability, and innovation. These manufacturers are shaping the future of the industry by continuously improving their production methods and expanding their market reach.
High-Quality Production: Indian industrial salt manufacturers are known for producing salt with high purity levels, making it suitable for various industrial applications. Their rigorous quality control measures ensure that the salt meets international standards, making it a preferred choice for global buyers.
Sustainable Practices: Sustainability is a key focus for many industrial salt manufacturers in India. By adopting eco-friendly production methods such as solar evaporation, they are reducing their environmental footprint and contributing to the long-term viability of the industry.
Innovation and Technology: The integration of advanced technologies has revolutionized the Indian industrial salt industry. Automation, digital monitoring, and precision harvesting techniques have enhanced production efficiency and product quality, allowing manufacturers to stay competitive in the global market.
4. The Role of Technology and Innovation
The adoption of advanced technologies and innovative practices has been instrumental in the growth of India’s industrial salt industry. Automation and digitalization have streamlined production processes, reducing labor costs and minimizing human error. These technologies also enable real-time monitoring of production, ensuring consistent quality and optimizing resource utilization.
Solar Evaporation: One of the most significant technological advancements in the industry is the use of solar evaporation. This method harnesses the abundant sunlight in regions like Gujarat and Tamil Nadu to evaporate seawater and extract salt. Solar evaporation is not only cost-effective but also environmentally friendly, as it requires minimal energy and produces high-purity salt with low environmental impact.
Precision Harvesting: Precision harvesting techniques have also gained popularity among industrial salt manufacturers in India. These techniques involve the use of machinery and sensors to monitor the crystallization process and harvest salt at the optimal time. This results in higher yields and better quality salt, which is crucial for meeting the demands of industrial applications.
5. Sustainability in Industrial Salt Production
Sustainability is becoming increasingly important in the industrial salt industry, with manufacturers taking steps to reduce their environmental impact. Sustainable production practices not only benefit the environment but also enhance the reputation of manufacturers in the global market.
Water Conservation: Water conservation is a key aspect of sustainable salt production. By optimizing water usage and recycling wastewater, manufacturers can significantly reduce their water footprint. This is particularly important in regions where water resources are scarce.
Waste Reduction: Minimizing waste is another critical component of sustainable production. Industrial salt manufacturers in India are implementing measures to reduce the amount of waste generated during the production process. This includes reusing by-products and implementing efficient waste management systems.
Renewable Energy: The use of renewable energy sources, such as solar and wind power, is also gaining traction in the industry. By reducing their reliance on fossil fuels, manufacturers are lowering their carbon emissions and contributing to the fight against climate change.
6. Export Potential and Global Market Reach
India’s industrial salt industry has significant export potential, with demand from various countries across Asia, Europe, and Africa. The combination of high-quality production and competitive pricing makes Indian industrial salt a preferred choice for international buyers.
Middle East Market: The Middle East is a major market for Indian industrial salt due to its growing chemical and petrochemical industries. The region’s demand for high-purity salt is met by India’s leading manufacturers, who have established strong distribution networks and partnerships with local companies.
Emerging Markets: Indian manufacturers are also exploring new markets in Africa and South America, where the demand for industrial salt is on the rise. These regions offer significant growth opportunities for India’s industrial salt industry, as they continue to industrialize and expand their manufacturing sectors.
7. Challenges Facing the Industry
Despite its strengths, the industrial salt industry in India faces several challenges. These include fluctuating raw material costs, environmental regulations, and competition from other salt-producing countries. Additionally, the industry is vulnerable to the impacts of climate change, such as rising sea levels and unpredictable weather patterns, which can affect salt production.
Raw Material Costs: The cost of raw materials, such as seawater and land for salt pans, can fluctuate due to factors like government policies and market demand. These fluctuations can impact the profitability of industrial salt manufacturers and make it challenging to maintain competitive pricing.
Environmental Regulations: Stricter environmental regulations are being imposed on the industrial salt industry to reduce its environmental impact. While these regulations are necessary for sustainability, they can also increase production costs and create compliance challenges for manufacturers.
Global Competition: The global market for industrial salt is highly competitive, with producers from other countries vying for market share. Indian manufacturers must continuously innovate and improve their production processes to stay competitive and meet the demands of international buyers.
FAQs
Q1: What are the primary uses of industrial salt?
A1: Industrial salt is mainly used in the production of chemicals like chlorine, caustic soda, and soda ash. It is also essential for water treatment, food preservation, and de-icing roads.
Q2: Why is India a leading producer of industrial salt?
A2: India has a vast coastline, favorable climatic conditions, and a skilled workforce, making it one of the largest producers of industrial salt. The country’s manufacturers are known for producing high-quality salt that meets global standards.
Q3: What sustainable practices are used in industrial salt production?
A3: Industrial salt manufacturers in India are adopting sustainable practices such as solar evaporation, water conservation, waste reduction, and the use of renewable energy sources to minimize their environmental impact.
Q4: How does solar evaporation work in salt production?
A4: Solar evaporation uses sunlight to evaporate seawater in large ponds, leaving behind salt crystals. This method is environmentally friendly and cost-effective, producing high-purity salt with minimal energy consumption.
Q5: What challenges does the industrial salt industry in India face?
A5: The industry faces challenges such as fluctuating raw material costs, environmental regulations, competition from other countries, and the impacts of climate change, which can affect production and profitability.