Understanding the Versatility of a 3 Jaw Chuck in Lathe Operations
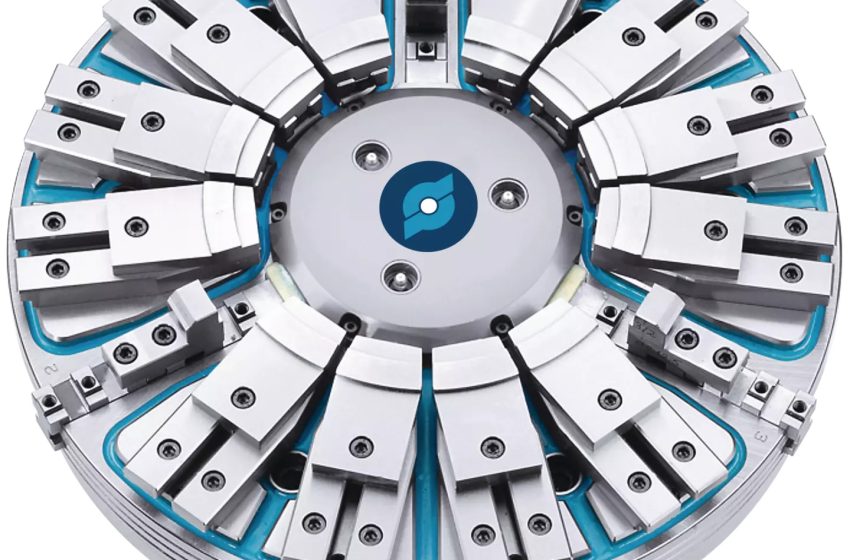
In the world of machining and manufacturing, precision and efficiency are essential for producing high-quality components. One of the most important tools in any lathe operation is the lathe chuck, a device that securely holds workpieces in place during machining. Among the different types of lathe chucks available, the 3 jaw chuck stands out as one of the most widely used due to its versatility, ease of use, and ability to center workpieces quickly.
This article explores the significance of the 3 jaw chuck, its applications, advantages, and how it enhances efficiency in lathe operations.
What is a 3 Jaw Chuck?
A 3 jaw chuck is a self-centering lathe chuck that features three equally spaced jaws, which move simultaneously when adjusted. This type of chuck is commonly used in both manual and CNC lathes to hold cylindrical or hexagonal workpieces securely. The jaws of the chuck are driven by a scroll plate, ensuring that the workpiece is automatically centered when tightened.
The 3 jaw chuck is particularly popular for turning operations that require quick and repetitive setups, making it ideal for mass production and general machining tasks.
How Does a 3 Jaw Chuck Work?
The 3 jaw chuck operates using a scroll mechanism, where all three jaws move inward or outward simultaneously when the chuck key is rotated. This design ensures that the workpiece is automatically centered, reducing the need for manual adjustments. The chuck is typically mounted on the spindle of the lathe and can be tightened or loosened to accommodate different sizes of workpieces.
Due to its self-centering nature, the 3 jaw chuck is ideal for machining cylindrical parts where precision alignment is crucial.
Advantages of Using a 3 Jaw Chuck in Lathe Operations
Self-Centering Feature
One of the biggest advantages of a 3 jaw chuck is its self-centering capability. When the jaws are tightened, they automatically align the workpiece in the center, ensuring uniformity in machining operations. This reduces setup time and minimizes errors, leading to consistent results.
Quick and Efficient Clamping
Compared to other types of lathe chucks, such as the 4-jaw independent chuck, the 3 jaw chuck allows for faster workpiece clamping. Since all three jaws move together, operators can secure the workpiece quickly, making it ideal for high-volume production.
Ideal for Round and Hexagonal Workpieces
The 3 jaw chuck is designed to grip round and hexagonal workpieces securely, making it suitable for applications such as turning, drilling, and boring. It provides even gripping force, ensuring that the workpiece remains stable during machining.
Reduced Risk of Workpiece Damage
Because the jaws of the 3 jaw chuck move simultaneously, they apply even pressure to the workpiece, reducing the risk of deformation or misalignment. This is particularly beneficial when working with delicate materials that require gentle but firm holding.
Compatibility with Manual and CNC Lathes
The 3 jaw chuck is widely used in both traditional manual lathes and modern CNC machines. This versatility makes it a preferred choice for machinists and manufacturers looking for a reliable lathe chuck for various machining applications.
Minimal Operator Effort Required
Unlike independent 4-jaw chucks that require manual adjustments to center the workpiece, the 3 jaw chuck does the job automatically. This reduces operator fatigue and allows machinists to focus on machining rather than workpiece alignment.
Applications of a 3 Jaw Chuck in Lathe Operations
The 3 jaw chuck is commonly used in a variety of machining applications, including:
General Turning Operations
Lathes equipped with a 3 jaw chuck are widely used for turning operations where cylindrical or hexagonal workpieces need to be machined with precision. The chuck holds the material securely while the cutting tool shapes it.
Drilling and Boring
In lathe operations that require drilling or boring, the 3 jaw chuck provides a stable grip on the workpiece, allowing for precise hole placement and depth control.
Facing and Chamfering
When performing facing and chamfering operations, the 3 jaw chuck ensures that the workpiece remains centered and stable, leading to accurate and smooth finishes.
Light Milling Operations
While primarily used for turning, some 3 jaw chucks can be adapted for light milling tasks in specialized applications. This makes them a flexible tool for machinists who require additional functionality from their lathe setups.
High-Speed Production
Industries that require high-speed and high-volume production, such as automotive and aerospace manufacturing, rely on 3 jaw chucks for their ability to quickly clamp and release workpieces with minimal downtime.
Limitations of a 3 Jaw Chuck
Despite its many advantages, the 3 jaw chuck does have some limitations:
-
Limited Adjustability: Unlike 4-jaw independent chucks, a 3 jaw chuck cannot hold irregularly shaped workpieces since all three jaws move together.
-
Lower Gripping Force: For heavy-duty machining or non-cylindrical parts, a 4-jaw chuck may be preferred for its higher clamping force and adjustability.
-
Not Suitable for Square or Asymmetrical Workpieces: The symmetrical design of the 3 jaw chuck limits its ability to securely grip non-uniform materials.
How to Maintain a 3 Jaw Chuck for Optimal Performance
Proper maintenance is essential to ensure the longevity and efficiency of a 3 jaw chuck. Here are some key maintenance tips:
Regular Cleaning: Metal shavings and debris can accumulate in the chuck mechanism, affecting its performance. Regular cleaning with compressed air and lubrication will prevent buildup.
Lubrication: Applying high-quality lubricant to the moving parts will ensure smooth operation and reduce wear.
Periodic Inspection: Checking for wear and tear on the jaws and scroll plate will help identify potential issues before they affect machining accuracy.
Proper Storage: When not in use, the 3 jaw chuck should be stored in a dry, clean environment to prevent rust and corrosion.
Conclusion
The 3 jaw chuck is an essential component in lathe operations, offering precision, efficiency, and ease of use. Its self-centering mechanism, quick clamping capabilities, and compatibility with various machining applications make it a preferred choice for both manual and CNC lathes.
For industries looking for high-quality lathe chuck solutions, Schunk provides advanced workholding technologies that enhance productivity and precision. With a reputation for innovation and excellence, Schunk’s 3 jaw chucks are designed to meet the demanding needs of modern manufacturing, ensuring superior performance in every machining operation.