Understanding the Environment of Injection Molding in China
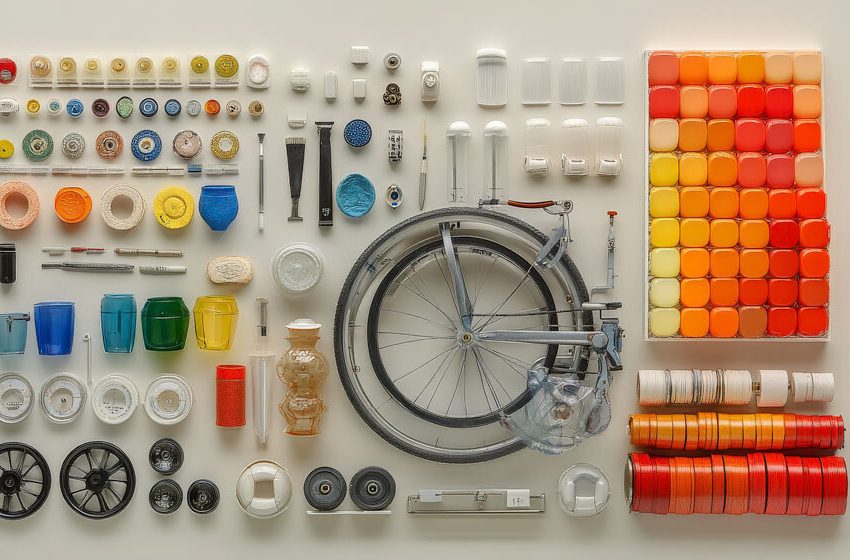
Injection molding in China is a manufacturing technique highly known for producing plastic and metal components. For many years now, these manufacturing companies have had a major impact on industries like automotive, electronics, and consumer goods.
Not unbeknownst to the world, China is the global frontrunner in manufacturing, injection molding in particular. The country’s dominance in this field is driven by its advanced production capabilities, cost efficiency, and swift adoption of new technologies. To further know more, we’ll be discussing trends, challenges, and opportunities within the industry. We’ll also give actionable insights for businesses aiming to source from this region. Let’s start!
Overview of Injection Molding in China
This manufacturing process enables the efficient production of precise components. In 2024, the market for this machine in China was valued at USD 3,178.2 million and is expected to grow at a compound annual growth rate (CAGR) of 6.2%, reaching USD 5,479.2 million by 2033. This growth is mainly driven by the increasing demand from industries such as automotive and packaging, coupled with advancements in manufacturing technologies.
Market Size
The injection molding market in China is characterized by strong leadership in both plastic and metal molding. This is caused by the integration of advanced technologies.
Industry 4.0 innovations, such as real-time monitoring and predictive maintenance, have greatly boosted production efficiency by cutting down on downtime and operating expenses. These technological advancements have solidified China’s position as a global leader in precision manufacturing. For this reason, the country leads in this industry.
Technological Advancements in Injection Molding
Industry 4.0 Integration
In China, injection molding has changed as a result of the implementation of Industry 4.0 technology. Automation, robotics, and cloud-based systems are being used more nowadays to improve production accuracy and efficiency.
For instance, ‘Go-factory cloud system’ allows for remote monitoring of operations, leading to smoother production workflows.
Energy Efficiency and Sustainability
With global warming and pollution affecting the planet, sustainability is now a top priority for Chinese manufacturers. Energy-efficient machines, like hybrid and electric models for instance, are gaining popularity for their lower energy consumption. Not to mention, without compromising precision. Added to that, using recyclable materials satisfies international environmental goals and appeals to people who care more about the environment.
Market Dynamics and Challenges
Shift in Manufacturing Preferences
Manufacturing tactics are changing due to worldwide developments including on-demand production and nearshoring. While these changes promote localized production for faster delivery times, China retains its competitive edge because of their advanced technologies and financial benefits. And compared to other areas, its vast supply chain network further improves efficiency.
Trade and Regulatory Challenges
The demand from important industries like electronics and automobiles has been impacted by the Sino-US trade war. What’s more, the high initial investment required for advanced machinery poses challenges for small- and medium-sized enterprises (SMEs). And a shortage of skilled labor also complicates the use of technologies like artificial intelligence (AI) and Internet of Things (IoT).
Strategic Sourcing from China
Evaluating Suppliers
When sourcing from China, businesses should assess suppliers based on their technological expertise, innovation capacity, and compliance with quality standards. Suppliers proficient in integrating Industry 4.0 technologies into their operations are particularly valuable and are more sought-after. An example of this would be companies that have AI-driven quality control systems that enhance precision while minimizing defects.
Ensuring Quality and Compliance
Strong quality control processes are essential when sourcing from China. Companies should require adherence to international standards like Advanced Product Quality Planning (APQP) and Production Part Approval Process (PPAP). Conducting regular audits will help maintain high standards while reducing any risks associated with remote sourcing.
Opportunities for Growth
Sustainability Initiatives
The growing emphasis on sustainability presents significant opportunities for China’s injection molding industry. Manufacturers are investing in environmentally friendly technologies that reduce energy usage and waste generation. Hybrid machines are particularly favored for their balance between efficiency and environmental responsibility.
Digital Transformation
Advanced technologies such as machine learning, digital twins, and real-time analytics are changing the industry processes by improving accuracy and reducing defect rates. These innovations lead to substantial cost savings. For instance, smart solutions enable manufacturers to meet stringent quality requirements across industries like automotive and electronics.
Regional Hubs Driving Growth
The market in China is thriving on the contributions of major cities like Shanghai, Shenzhen, Guangzhou, Beijing, and Tianjin. When it comes to automotive and electronics production, Shanghai is a key player. They leverage their modern facilities to enable advanced manufacturing.
In Shenzhen, the focus lies on creating intricate electronic parts integral to modern devices such as smartphones. Guangzhou on the other hand has positioned itself as a leader in lightweight automotive parts production. And as for Beijing, they emphasize innovation through research initiatives backed by government policies aimed at technological growth.
Key Takeaway
Injection molding in China is on the threshold of considerable growth, propelled by technological advancements, sustainability efforts, and strong demand from key industries like automotive and electronics. That being said, challenges such as trade disputes and the high upfront costs of advanced machinery persist. Despite these hurdles, the country remains integral in global manufacturing.
Companies sourcing from China can improve their supply chains by capitalizing on cost advantages while maintaining stringent quality control protocols. Success will depend on suppliers with strong technological expertise and adherence to international standards. Thus, making sure a reliable and efficient partnership is formed.