Taming the Label Tango: How to Troubleshoot Common Label Printer Problems
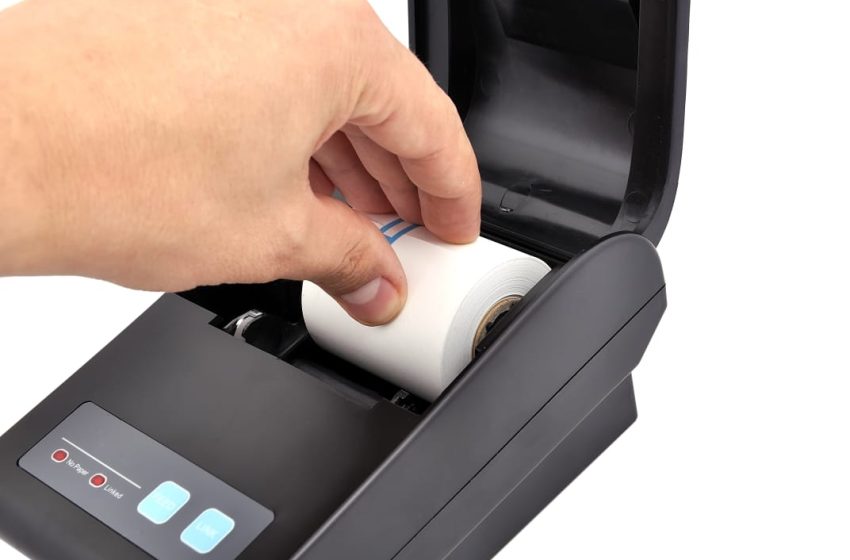
Taming the Label Tango: How to Troubleshoot Common Label Printer Problems
Label printers are fantastic tools for keeping your home or office organized. They help you create personalized labels for everything from storage containers to mailing addresses. But like any other machine, label printers can sometimes act up. Don’t worry, throwing your printer in frustration isn’t the answer!
This blog is here to guide you through troubleshooting common label printer problems, getting you back to creating crisp, clear labels in no time.
We’ll break down the issues into two categories:
-
Printing Problems: These deal with the quality or output of your labels.
-
Feeding Problems: These involve issues with the labels themselves entering the printer correctly.
For each problem, we’ll explore potential causes and simple solutions you can try at home.
Printing Problems
1. Blurry or Faint Print
Cause: This could be due to several factors:
-
Low ink/ribbon: For thermal transfer printers, check the ribbon for ink depletion. Inkjet printers require a refill of ink cartridges.
-
Dirty print head: Dust and debris buildup on the print head can obstruct proper ink transfer.
-
Incorrect print settings: Resolution (DPI) might be too low, or settings might not match your label type.
Solution:
-
Replace the ink ribbon or refill ink cartridges as needed (consult your printer’s manual for specific instructions).
-
Clean the print head using the method recommended by your label printer Qatar manufacturer (often involving cleaning swabs and isopropyl alcohol).
-
Check your print settings and ensure they match your label type (e.g., glossy labels might require a higher DPI setting). Most label printing software offers presets for different label materials.
2. Spots or Streaks on Labels
Cause: This is often caused by:
-
Clogged print head nozzles: Similar to blurry prints, clogged nozzles can disrupt ink flow, leading to uneven printing.
-
Damaged print head: In rare cases, the print head itself might be malfunctioning.
-
Solution:
-
Perform a more thorough print head cleaning as recommended by your manufacturer. This might involve using a dedicated cleaning solution or running an automated cleaning cycle on your printer.
-
-
If cleaning doesn’t resolve the issue, consult your printer’s manual or manufacturer’s support for troubleshooting a potentially damaged print head.
3. Labels Not Printing Edge-to-Edge
Cause: This can happen due to:
-
Incorrect margins or layout settings: Your label design software might have margins set too wide, preventing the entire design from being printed.
-
Printer calibration issues: The printer itself might not be feeding the labels accurately.
Solution:
-
Double-check your margins and layout settings in your label design software. Ensure they match the exact dimensions of your labels.
-
Most label printers offer calibration options. Refer to your printer’s manual to find the calibration process specific to your model. This might involve feeding a blank label through the printer and following on-screen prompts.
4. Ink/Toner Transferring to Other Labels
Cause: This can occur because of:
-
Wet ink: Freshly printed labels might touch each other before the ink dries completely, causing smudging.
-
Incorrect label material: Labels might not be designed for your specific printer type (e.g., using inkjet labels in a laser printer).
Solution:
-
Allow freshly printed labels to dry completely before stacking or touching them.
-
Ensure you’re using the correct label type for your printer. Inkjet labels require different materials than laser toner labels. Check your printer’s manual or label packaging for compatibility information.
Feeding Problems
1. Labels Not Feeding Properly
-
Cause: This could be due to:
-
Incorrect label size or type: Labels might be too large, too small, or not designed for automatic feeding.
-
Curled or damaged labels: Improper storage can cause labels to curl or stick together, hindering smooth feeding.
-
Dirty or worn feed rollers: Dust buildup or worn rollers can affect the printer’s grip on the labels.
-
Solution:
-
Double-check that your labels match the size and type recommended by your printer manufacturer. Most printers specify compatible label dimensions in their user manuals.
-
Store your labels flat and cool to prevent curling or sticking.
-
Gently clean the feed rollers with a lint-free cloth to remove dust or debris. Some printers allow for removal of the rollers for a more thorough cleaning (refer to your manual).
2. Label Jams
-
Cause: Label jams are often caused by:
-
Misaligned labels: Labels might be crooked or not feeding straight into the printer.
-
Foreign objects: Small objects like paperclips or debris might be stuck inside the printer, causing jams.
-
Damaged labels: Ripped, torn, or crumpled labels can easily get stuck during feeding.
-
Solution:
-
Carefully open the printer and remove any jammed labels. Be gentle to avoid tearing the labels or damaging the printer mechanism. Refer to your printer’s manual for specific instructions on opening the printer safely.
-
Check for any misaligned labels and straighten them before feeding.
-
Gently inspect the printer’s interior for any foreign objects that might be causing obstructions.
-
Discard any damaged labels and use fresh ones.
3. Labels Printing Off-Center
-
Cause: This can happen due to:
-
Incorrect label alignment settings: Your label printing software might have mismatched alignment settings for your specific labels.
-
Skewed labels: Labels might be slightly askew within the feeder tray.
-
Solution:
-
In your label design software, locate the alignment settings and ensure they match the dimensions of your labels. Most software offers visual guides to help you set these correctly.
-
-
Before feeding the labels, visually check if they are sitting straight within the feeder tray.
General Tips for Smooth Label Printing
-
Always consult your printer’s manual: The manufacturer’s manual is your best resource for troubleshooting specific issues related to your printer model. It will provide detailed instructions on cleaning, calibration, and compatible label types.
-
Invest in high-quality labels: Using labels specifically designed for your printer type can significantly reduce feeding problems and ensure optimal print quality.
-
Update printer drivers: Outdated drivers might cause compatibility issues with your label printing software. Check your printer manufacturer’s website for the latest driver updates.
-
Test printing a single label first: Before printing a large batch, do a test print on a single label to ensure everything is functioning correctly. This saves you time and wasted labels in case of any issues.
-
Restart your printer and computer: Sometimes a simple restart can resolve temporary glitches that might be causing printing problems.
Conclusion
By following these tips and troubleshooting steps, you can overcome the most common label printer problems and get back to creating professional-looking labels with ease. Bear in mind that if you encounter a complex issue beyond your comfort level, don’t hesitate to consult your printer’s manufacturer support for further assistance.