Solid Carbide: The Ideal Material for Manufacturers
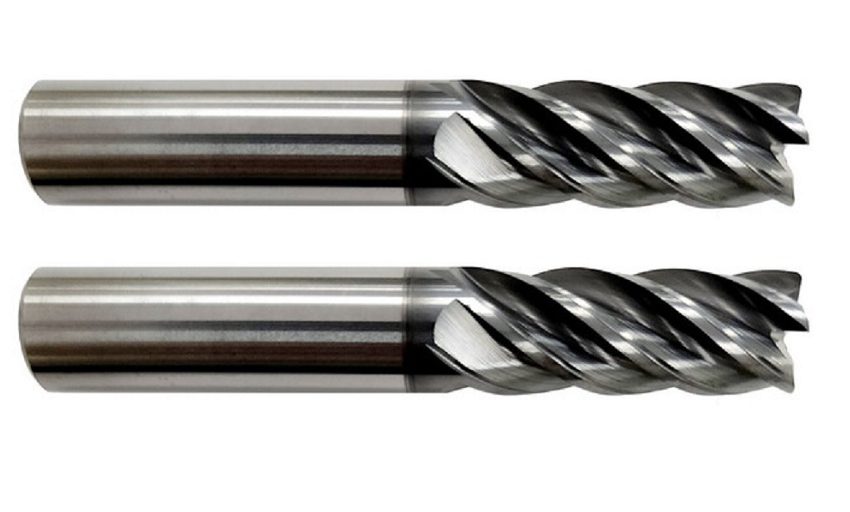
The manufacturing business has used all sorts of materials since the beginning of the industrial revolution. And iron and steel has shaped most of what the modern world is now. However, the search for the strongest and toughest materials has never stopped, and in the mid 20th century the discovery of solid carbide has only made the march of progress faster.
Solid carbide, a versatile material renowned for its exceptional properties, finds extensive applications across various industries. From cutting tools to wear parts, its utilization has become ubiquitous in modern manufacturing processes.
The qualities of solid carbide make it stand out and why carbide drill manufacturers know it’s the best material to create tools for high speed and precision machining.
Properties
Solid carbide was already known and discovered since the late 19th century. It was already recognized for its hardness and durability, but it wasn’t until it was used as a cutting tool and as a way to resize the filaments in light bulbs that it found its niche in the manufacturing industry.
Also known as tungsten carbide, it is a composite material composed of tungsten carbide particles held together by a metallic binder, typically cobalt. This unique composition results in a material that exhibits remarkable hardness, toughness, and wear resistance, making it ideal for demanding industrial applications.
The Hardest Tool Material?
One of the key properties of solid carbide is its exceptional hardness, ranking higher than traditional materials like steel. This hardness enables carbide tools to withstand high temperatures and abrasive wear, ensuring prolonged tool life and enhanced performance.
It may not be the hardest material, as diamond is still the hardest of all, but solid carbide can withstand extreme pressures and temperatures. It also has the sufficient toughness to endure heavy loads and shock loads without fracturing.
This makes it ideal for withstanding the rigorous conditions encountered in machining and cutting operations, which many industries require for their operations.
Wear Resistance
Solid carbide’s superior wear resistance is attributed to its hard carbide particles dispersed within the metallic binder. This resistance to wear ensures minimal tool degradation over prolonged use, leading to consistent and precise machining results.
Solid carbide drill manufacturers add to this wear and tear resistance by adding a coating to their tools made of solid carbide. These coatings can be made from titanium aluminum nitride (TiAIN), titanium carbonitride (TICN), or even diamond-like carbon (DLC).
The Various Applications of Solid Carbide
Solid carbide finds extensive applications across various industries, owing to its exceptional properties and versatility. However, it wasn’t so clear from the start. Though many scientists and researchers found solid carbide a stunning material, very few knew how it can be used.
Though it had its stint in the industry of war during the mid 20th century, the use of solid carbide these days is limited to the creation of high precision tools and accessories that need to be resistant to scratch and high in durability.
Cutting Tools
Carbide drill manufacturers use carbide to make cutting tools, including drills, end mills, and inserts. These are widely used in machining operations across industries such as aerospace, automotive, and medical. The hardness and wear resistance of solid carbide make it ideal for cutting and shaping hard materials like steel, titanium, and composites.
Wear Parts
In industries where abrasive wear is a concern, solid carbide components, such as seals, bearings, and nozzles, offer superior durability and longevity compared to traditional materials. These wear parts ensure reliable performance and reduced downtime in critical applications.
Automotive and Industrial Machinery
Solid carbide is also employed in the manufacturing of industrial machinery components, such as gears, dies, and molds. Its ability to withstand high temperatures and abrasive wear makes it indispensable in applications requiring precision and reliability.
The Material for Modern Precision
Solid carbide continues to reign supreme as the material of choice for a myriad of industrial applications, thanks to its exceptional properties and myriad benefits. From cutting tools to wear parts, its versatility and performance efficiency make it indispensable for manufacturers striving for excellence in precision machining.
For more information about Chamfer Mills and Stub Drills please visit:- Online Carbide