Production Cost of Calcined Zeolite: A Comprehensive Exploration of Prices, Trends & Forecasts
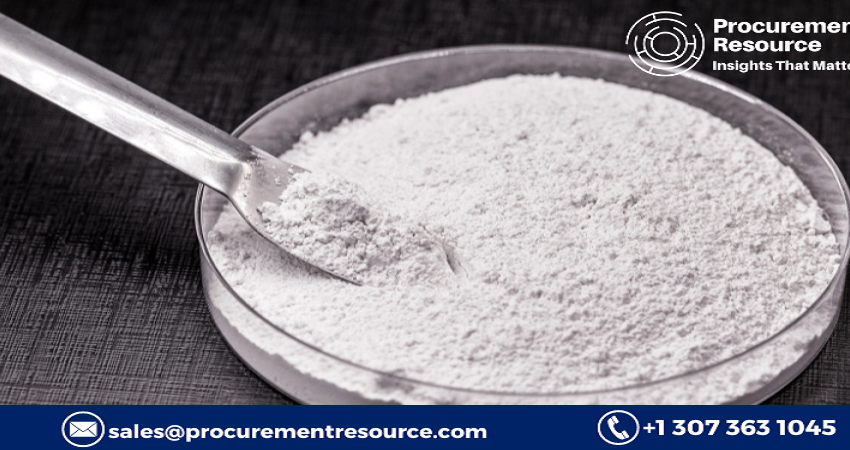
Calcined zeolite, a versatile material with diverse applications in industries such as petrochemicals, environmental remediation, and agriculture, is renowned for its adsorption, catalytic, and ion exchange properties. Understanding the intricacies of its production cost is essential for manufacturers and stakeholders aiming to optimize cost-effectiveness while maintaining product quality and market competitiveness. In this comprehensive guide, we delve into the multifaceted aspects influencing the Production Cost of Calcined Zeolite, providing insights and strategies to navigate the complexities of zeolite manufacturing.
Introduction to Calcined Zeolite
Calcined zeolite, derived from natural or synthetic zeolite minerals through controlled heating or calcination processes, exhibits enhanced thermal stability, porosity, and surface area compared to its precursor forms. It finds widespread applications as catalysts, adsorbents, soil amendments, and water treatment media due to its unique structural properties and high surface reactivity. The production cost of calcined zeolite plays a pivotal role in determining its market viability and suitability for various industrial and environmental applications.
Request For Free Sample: https://www.procurementresource.com/production-cost-report-store/calcined-zeolite/request-sample
Factors Influencing Production Cost
Raw Material Procurement
The production cost of calcined zeolite is closely tied to the sourcing and pricing of raw materials, primarily natural zeolite minerals or synthetic zeolite powders. Factors such as zeolite composition, purity, particle size, and geographical location impact the cost and availability of raw materials for calcination. Zeolite deposits, mining operations, and mineral processing facilities play a crucial role in ensuring a consistent and quality supply chain. Strategic partnerships, mineral rights agreements, and quality assurance protocols mitigate raw material supply risks and production costs.
Calcination Process
Calcined zeolite production involves heating natural or synthetic zeolite minerals to high temperatures (typically above 500°C) to remove water molecules and induce structural changes, resulting in increased thermal stability and surface area. The choice of calcination method, heating rate, temperature profile, and residence time significantly influences production costs, product yield, and physicochemical properties. Continuous process optimization, kiln design improvements, and energy-efficient heating technologies enhance calcination efficiency and reduce energy consumption. Innovative calcination techniques such as microwave heating, fluidized bed reactors, and rotary kilns offer opportunities for cost reduction and process innovation.
Energy Consumption
Energy-intensive calcination processes contribute to the overall production cost of calcined zeolite. Energy costs, including electricity, natural gas, and fossil fuels, constitute a significant portion of the operating expenses in zeolite calcination facilities. Adopting energy-efficient heating systems, waste heat recovery technologies, and renewable energy sources optimize energy utilization and reduce production costs. Energy management programs, operational optimization, and energy audits identify opportunities for efficiency improvements and cost savings in calcined zeolite production.
Market Dynamics
Demand-Supply Dynamics
The production cost of calcined zeolite is influenced by demand-supply dynamics in industries such as petrochemicals, environmental engineering, agriculture, and water treatment. Fluctuations in market demand, regulatory standards, and technological advancements impact market dynamics and product pricing. Growing demand for zeolite-based catalysts, adsorbents, and soil conditioners drives demand for calcined zeolite products. Adapting to changing market conditions, customer requirements, and emerging applications is essential for managing production costs and maintaining competitiveness in the zeolite market.
Price Volatility
Calcined zeolite prices are subject to volatility due to factors such as raw material costs, supply-demand imbalances, and macroeconomic trends. The cyclical nature of the mineral industry, geopolitical events, and changes in currency exchange rates impact production costs and profit margins for zeolite producers. Risk management strategies, such as hedging, price indexing, and inventory management, help mitigate price volatility and financial risks associated with zeolite production. Long-term supply agreements, strategic inventory planning, and market intelligence initiatives provide stability and resilience in volatile market conditions.
Cost Optimization Strategies
Process Efficiency Improvements
Continuous process optimization initiatives enhance efficiency, productivity, and cost-effectiveness in calcined zeolite production. Employing advanced process modeling tools, data analytics, and real-time monitoring systems optimize calcination parameters, heating profiles, and equipment performance. Integration of automation, control systems, and advanced sensors enhances process reliability and product consistency. By-product utilization, waste minimization, and resource recovery strategies optimize resource utilization and reduce production costs.
Supply Chain Optimization
Efficient supply chain management practices optimize raw material procurement, logistics, and inventory management processes, thereby reducing costs and enhancing operational efficiency. Collaborating with reliable suppliers, implementing demand forecasting systems, and optimizing transportation logistics streamline supply chain operations. Digitalization, blockchain technology, and data-driven analytics enhance supply chain visibility, transparency, and resilience. Just-in-time inventory management, vendor consolidation, and strategic partnerships mitigate supply chain risks and reduce production costs.
Innovation and Product Development
Investments in research and development (R&D) drive technological innovation and product development in calcined zeolite production. Collaborative R&D partnerships, government grants, and industry consortia support the development of novel calcination techniques, zeolite formulations, and value-added applications. Emerging technologies such as chemical vapor deposition, surface modification, and functionalization offer opportunities for cost reduction and product differentiation. Customer feedback, market research, and application testing guide product innovation efforts and market positioning strategies.
Conclusion
In conclusion, the production cost of calcined zeolite is influenced by various factors, including raw material procurement, calcination processes, energy consumption, market dynamics, and cost optimization strategies. Manufacturers of calcined zeolite face the challenge of balancing cost-effectiveness with product quality, regulatory compliance, and market competitiveness. By understanding these factors and implementing targeted cost optimization strategies, zeolite producers can navigate the complexities of calcined zeolite manufacturing, enhance profitability, and meet the evolving needs of industries and environmental applications.