Explore the Production Cost of Aluminium
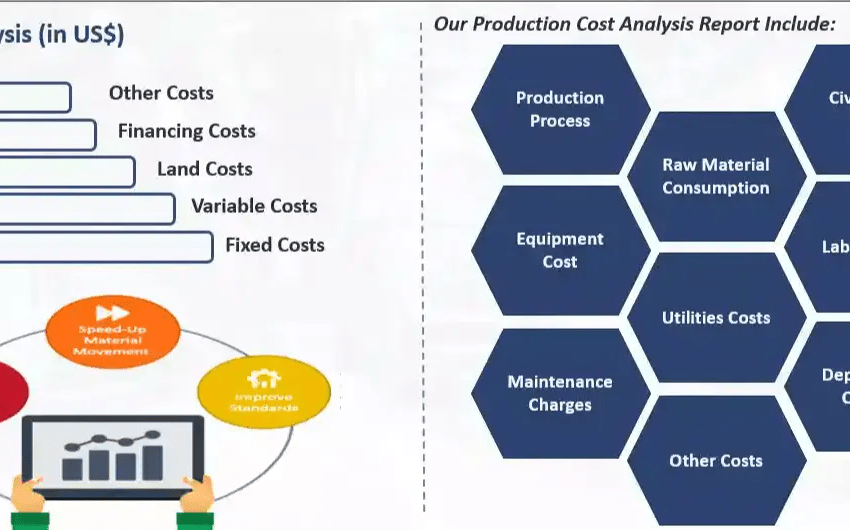
Aluminium, known for its lightweight, corrosion-resistant, and recyclable properties, is one of the most widely used metals across various industries. From automotive and aerospace to construction and packaging, Aluminium Production Cost, finds applications in a diverse range of products and processes. However, the production of aluminium involves complex processes and costs that can fluctuate due to several factors. In this article, we explore the Production Cost of Aluminium, shedding light on key cost drivers, recent trends, and strategies to optimize production expenses.
Understanding Aluminium Production Cost
Aluminium production costs encompass various components, including:
1. Raw Material Costs
- Bauxite Prices: Bauxite is the primary source of aluminium, and its prices are influenced by factors such as mining output, quality of bauxite reserves, transportation costs, and geopolitical factors affecting mining operations.
- Alumina Prices: Alumina, extracted from bauxite through the Bayer process, serves as the intermediate product in aluminium production. Fluctuations in alumina prices are driven by factors like refining capacity, energy costs, environmental regulations, and market demand.
- Energy Costs: Aluminium smelting is energy-intensive, with electricity accounting for a significant portion of production expenses. Variations in energy prices, influenced by factors such as fuel costs, regulatory policies, and renewable energy adoption, impact overall production costs.
2. Production Processes
- Smelting Technology: The choice of smelting technology, whether it’s the Hall-Héroult process or newer innovations like inert anode technology, affects energy efficiency, productivity, and operational costs.
- Labour and Operating Expenses: Labour costs, maintenance expenses, and overheads associated with operating aluminium smelters contribute to overall production costs.
3. Market Dynamics
- Global Demand and Supply: Fluctuations in aluminium demand, driven by economic growth, industrial activity, and consumer preferences, influence market prices and production volumes. Supply-demand imbalances, trade policies, and geopolitical tensions also impact aluminium prices.
- Currency Exchange Rates: Aluminium is a globally traded commodity, and exchange rate fluctuations can affect the competitiveness of producers in different regions. Currency movements against the US dollar can influence the cost of imported raw materials and equipment.
Request For Free Sample: https://www.procurementresource.com/production-cost-report-store/aluminum/request-sample
Recent Trends in Aluminium Production Costs
1. Energy Efficiency Initiatives
- Renewable Energy Adoption: Aluminium producers are increasingly investing in renewable energy sources such as hydroelectric, solar, and wind power to reduce carbon emissions and mitigate exposure to fossil fuel price volatility. Transitioning to renewable energy can enhance energy security and reduce long-term production costs.
- Energy Recovery Technologies: Implementation of energy recovery systems and process improvements, such as waste heat recovery and cogeneration, helps optimize energy usage and minimize production costs.
2. Sustainability and Environmental Compliance
- Emission Reduction Measures: Stringent environmental regulations and carbon pricing mechanisms incentivize aluminium producers to invest in emission control technologies, carbon capture and storage (CCS) systems, and low-carbon production processes. While these initiatives entail initial capital expenditure, they help mitigate regulatory risks and enhance the long-term sustainability of operations.
- Recycling and Circular Economy: Promoting aluminium recycling and closed-loop material flows reduces the reliance on primary production from bauxite and lowers energy consumption and costs associated with virgin aluminium production. Embracing a circular economy approach fosters resource efficiency and cost competitiveness.
Strategies to Optimize Aluminium Production Costs
1. Supply Chain Optimization
- Supplier Relationships: Collaborating closely with bauxite and alumina suppliers to secure stable and competitive pricing arrangements can mitigate supply chain risks and volatility in raw material costs.
- Logistics Efficiency: Streamlining logistics operations, optimizing transportation routes, and leveraging digital technologies for supply chain visibility and real-time monitoring help minimize transportation costs and improve inventory management.
2. Technological Innovation
- Process Optimization: Continuous improvement initiatives, data analytics, and predictive maintenance technologies optimize smelting processes, enhance equipment reliability, and reduce downtime, thereby lowering production costs.
- Advanced Smelting Technologies: Investing in state-of-the-art smelting technologies, such as advanced cell designs, inert anode systems, and electrolytic innovations, improves energy efficiency and productivity, driving down per-unit production costs.
Conclusion
Aluminium production costs are influenced by a myriad of factors, including raw material prices, energy expenses, technological advancements, market dynamics, and regulatory compliance requirements. Proactive management of these cost drivers, coupled with strategic investments in renewable energy, sustainability initiatives, and technological innovation, enables aluminium producers to enhance competitiveness, profitability, and resilience in the global market. By embracing a holistic approach to cost optimization and sustainable practices, the aluminium industry can navigate challenges and capitalize on opportunities for long-term growth and value creation.
About Industry Insights
Industry Insights is a leading provider of market intelligence and analysis for the industrial sector. With a focus on delivering actionable insights and strategic recommendations, our team of industry experts helps businesses thrive in today’s rapidly evolving market environment. Whether you’re a manufacturer, distributor, investor, or