Bridge Machining Centers: Enhancing Efficiency in Manufacturing
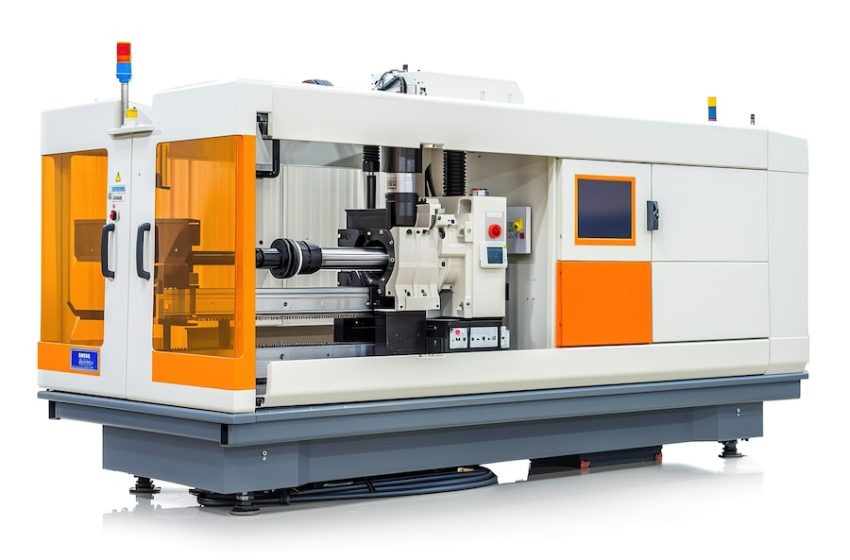
In the ever-evolving world of manufacturing, efficiency and precision are paramount. One of the key technologies that have emerged to address these demands is the bridge machining center. Renowned for their versatility and robust capabilities, bridge machining centers are transforming the landscape of modern manufacturing. In this blog, we will explore what bridge machining centers are, their benefits, applications, and how they enhance efficiency in manufacturing processes.
What is a Bridge Machining Center?
A bridge machining center is a type of CNC (Computer Numerical Control) machine characterized by its unique design. Unlike traditional machining centers, bridge machines feature a fixed bridge structure that supports the spindle, allowing for precise movement along the X, Y, and Z axes. This design provides enhanced stability and rigidity, making it ideal for machining large and complex workpieces.
Key Features
- Stability and Rigidity: The bridge design minimizes vibration during machining, which is crucial for achieving high precision.
- Large Working Envelope: Many bridge machining centers offer expansive working areas, accommodating larger parts that may not fit in standard machines.
- Multi-Axis Machining: Advanced models can operate on multiple axes simultaneously, increasing the complexity of parts that can be produced.
Benefits of Bridge Machining Centers
1. Increased Efficiency
One of the most significant advantages of bridge machining centers is their ability to enhance efficiency. Their design allows for faster machining cycles and reduced setup times. This means that manufacturers can produce more parts in less time, which is critical in today’s competitive landscape.
2. High Precision and Quality
The rigidity of bridge machining centers ensures that even the most intricate designs are produced with exceptional accuracy. This high level of precision reduces the need for rework and scrap, ultimately saving costs and time.
3. Versatility in Applications
Bridge machining centers are suitable for a wide range of materials, including metals, plastics, and composites. This versatility makes them an excellent choice for industries such as aerospace, automotive, and mold-making, where complex geometries are common.
4. Reduced Labor Costs
With automated CNC technology, bridge machining centers require less manual intervention compared to traditional machining processes. This automation not only speeds up production but also reduces labor costs, allowing skilled workers to focus on more strategic tasks.
5. Enhanced Tooling Options
Many modern bridge machining centers come equipped with advanced tooling options, such as automatic tool changers and integrated probing systems. These features allow for seamless transitions between different machining tasks, further boosting productivity.
Applications of Bridge Machining Centers
Bridge machining centers are utilized across various industries due to their adaptability and precision. Here are some common applications:
1. Aerospace Industry
In the aerospace sector, components must meet strict safety and performance standards. Bridge machining centers are used to manufacture parts like aircraft frames, engine components, and landing gear with high precision and reliability.
2. Automotive Manufacturing
From engine blocks to complex suspension parts, the automotive industry relies on bridge machining centers to produce intricate components that require tight tolerances. Their ability to handle large workpieces makes them ideal for this application.
3. Mold and Die Making
Bridge machining centers are essential in the mold-making industry, where complex shapes and fine details are critical. They allow manufacturers to create high-quality molds for plastics, metals, and other materials, ensuring efficient production runs.
4. Medical Device Manufacturing
The medical industry demands precision and consistency. Bridge machining centers are used to produce components for surgical instruments, implants, and diagnostic equipment, ensuring that each part meets stringent quality standards.
Choosing the Right Bridge Machining Center
When selecting a bridge machining center for your manufacturing needs, consider the following factors:
1. Size and Working Envelope
Assess the size of the components you plan to machine. Choose a center with an appropriate working envelope to accommodate your largest workpieces.
2. Axis Configuration
Determine how many axes you need. For more complex geometries, a machine with multiple axes will be essential.
3. Control System
Look for a bridge machining center equipped with a user-friendly CNC control system. Advanced controls with intuitive interfaces can simplify operations and reduce training time.
4. Tooling Compatibility
Ensure that the machining center is compatible with the tooling options you require. The ability to integrate various tools can enhance flexibility and productivity.
5. Manufacturer Support
Consider the level of support and service offered by the manufacturer. A reliable supplier will provide training, maintenance, and prompt assistance when issues arise.
Conclusion
Bridge machining centers are revolutionizing the manufacturing industry by enhancing efficiency, precision, and versatility. Their unique design and advanced features allow manufacturers to produce complex parts quickly and accurately, making them a valuable asset in various sectors, from aerospace to automotive. By investing in a high-quality bridge machining center, businesses can not only improve their production capabilities but also stay competitive in an increasingly demanding marketplace