The Ultimate Guide to Injection Molding: Techniques and Benefits
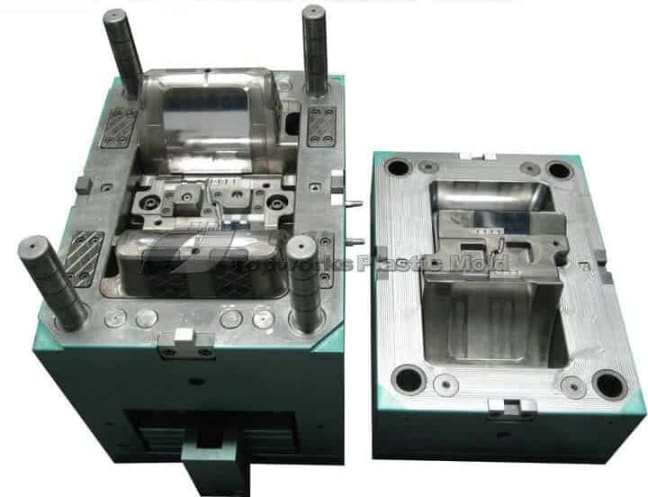
Injection molding is a vital process in modern manufacturing, enabling the creation of complex parts with precision and efficiency. This guide will explore various aspects of injection molding, including its techniques, benefits, and applications. Whether you’re a seasoned professional or new to the industry, this article will provide valuable insights.
What is Injection Molding?
Injection molding is a manufacturing process used to produce parts by injecting molten material into a mold. This technique is widely used for creating plastic components but can also be applied to metals and ceramics.
How Does Injection Molding Work?
The injection molding process involves several steps:
- Material Preparation: The raw material, usually in the form of pellets, is heated until it becomes molten.
- Injection: The molten material is injected into a mold under high pressure.
- Cooling: The material cools and solidifies in the mold.
- Ejection: Once cooled, the mold opens, and the finished part is ejected.
Understanding these steps is crucial for optimizing the injection molding process.
Benefits of Injection Molding
Injection molding offers numerous advantages, making it a preferred choice for many manufacturers. Here are some key benefits:
- High Efficiency: The process allows for mass production of identical parts, reducing manufacturing time.
- Precision: Injection molding produces parts with tight tolerances, ensuring quality and consistency.
- Material Versatility: Various materials can be used, including thermoplastics, thermosets, and metals.
- Complex Geometries: The technique can create intricate designs that would be difficult or impossible with other manufacturing methods.
- Reduced Waste: The process minimizes material waste, as excess material can often be recycled.
Applications of Injection Molding
Injection molding finds applications across various industries, including:
- Automotive: Parts such as dashboards, bumpers, and interior components.
- Consumer Goods: Items like containers, toys, and household appliances.
- Medical Devices: Components for syringes, surgical instruments, and diagnostic equipment.
- Electronics: Housings for devices, connectors, and components.
Understanding these applications can help businesses identify opportunities for using injection molding in their operations.
Key Techniques in Injection Molding
Several techniques enhance the injection molding process, each with its unique benefits:
1. Multi-Shot Injection Molding
This technique involves injecting different materials into the same mold to create multi-material parts. It allows for:
- Enhanced Functionality: Combining materials can improve product performance.
- Aesthetic Appeal: Different colors and textures can be achieved in a single part.
2. Gas-Assisted Injection Molding
In this method, gas is injected into the mold to create hollow sections in the part. Benefits include:
- Weight Reduction: Hollow parts are lighter, which is advantageous for many applications.
- Material Savings: Less material is required, reducing costs.
3. Insert Molding
This technique integrates metal or other components into the molded part. Advantages include:
- Improved Strength: Combining materials can enhance the overall strength of the final product.
- Reduced Assembly Time: Fewer parts mean quicker assembly and reduced labor costs.
Choosing the Right Injection Molding Partner
When selecting an injection molding supplier, consider the following factors:
- Experience: Look for companies with a proven track record in the industry.
- Technology: Ensure they use advanced machinery and techniques for optimal results.
- Quality Assurance: A robust quality control process is essential for maintaining standards.
Table: Factors to Consider When Choosing a Supplier
Factor | Description |
---|---|
Experience | Years in the industry and past projects |
Technology | Machinery and techniques used |
Quality Assurance | Processes in place for quality control |
Customer Support | Responsiveness and support offered to clients |
Pricing | Competitive pricing without compromising quality |
Common Challenges in Injection Molding
While injection molding is highly effective, it does come with its challenges:
- Tooling Costs: Initial mold creation can be expensive, impacting small production runs.
- Cycle Time: Optimizing cycle time can be complex, requiring careful adjustments.
- Material Selection: Choosing the wrong material can lead to product failures.
Addressing these challenges is crucial for successful injection molding operations.
Future Trends in Injection Molding
The injection molding industry is evolving, with several trends shaping its future:
- Sustainability: Increased focus on eco-friendly materials and processes.
- Automation: Advanced robotics and AI are streamlining production.
- Customization: Growing demand for customized products is driving innovation.
Staying informed about these trends can help businesses remain competitive.
Conclusion
Injection molding is a powerful manufacturing technique that offers numerous benefits, from efficiency to precision. Understanding its processes, applications, and future trends can help businesses leverage this technology effectively. For more information on leading suppliers, check out top manufacturers of injection molds in China or explore the benefits of finding injection molding services near you.